urumomo
Well-Known Member
- Joined
- Mar 18, 2013
- Messages
- 6,815
With all the talk about spray booths ,
I figure I'll share what I built around 9 years ago .
I know this is more elaborate than most people want to involve themselves in ( possibly ) , but the suction coming from beneath the work allows me to spray without being encumbered by surrounding bulkheads and a lid , and the 2 X 4 foot size was chosen to accommodate large builds .
Construction pics :
View from beneath .
Basically a shallow , rectangular box with a suction plenum below .
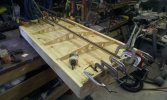
Now flipped upright .
Transverse strips are added . They are free to slide back and forth lengthwise .
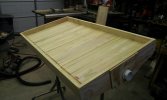
Then longitudinal strips are placed over the transverse strips .
They are also able to slide back and forth .
Then , with the transverse strips in the " open " position ( note the wire handles are protruding )
and the longitudinal strips in the " closed " position ( their wire handles , or push rods , are pushed into the box )
Holes are then drilled completely through both layers of strips and the bottom panel of the box
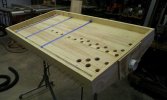
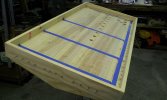
Lots of drilling
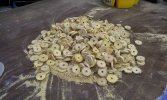
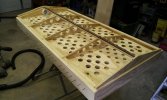
With transverse strips pushed in to the closed position :
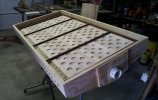
With some of the transverse strips pulled open and all the longitudinal strips pushed in :
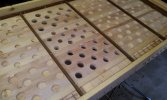
Then with some of the longitudinal strips pulled out , it will close off the corresponding holes that are opened by the transverse strips .
This allows for the suction zone to be tailored for the task at hand .
It allows the air flow to remain high where it is needed most :
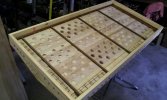
Partial openings can be created for fine tuning if needed :
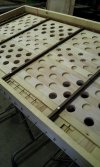
The suction connection and single mounting point to anchor the table in place :
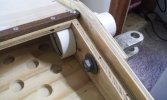
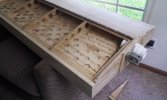
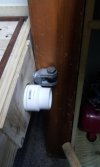
The table can swing and rotate about this single connector . The work top can be level or angled .
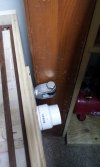
Fitted with standard A/C filters :
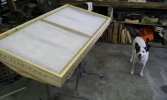
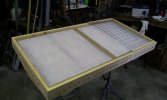
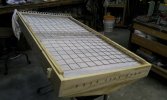
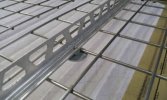
I figure I'll share what I built around 9 years ago .
I know this is more elaborate than most people want to involve themselves in ( possibly ) , but the suction coming from beneath the work allows me to spray without being encumbered by surrounding bulkheads and a lid , and the 2 X 4 foot size was chosen to accommodate large builds .
Construction pics :
View from beneath .
Basically a shallow , rectangular box with a suction plenum below .
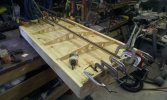
Now flipped upright .
Transverse strips are added . They are free to slide back and forth lengthwise .
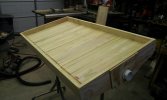
Then longitudinal strips are placed over the transverse strips .
They are also able to slide back and forth .
Then , with the transverse strips in the " open " position ( note the wire handles are protruding )
and the longitudinal strips in the " closed " position ( their wire handles , or push rods , are pushed into the box )
Holes are then drilled completely through both layers of strips and the bottom panel of the box
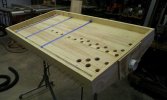
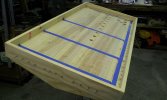
Lots of drilling
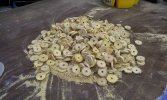
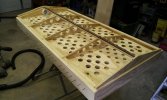
With transverse strips pushed in to the closed position :
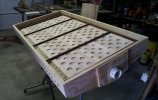
With some of the transverse strips pulled open and all the longitudinal strips pushed in :
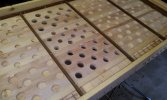
Then with some of the longitudinal strips pulled out , it will close off the corresponding holes that are opened by the transverse strips .
This allows for the suction zone to be tailored for the task at hand .
It allows the air flow to remain high where it is needed most :
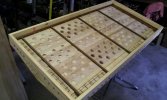
Partial openings can be created for fine tuning if needed :
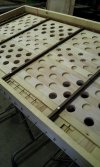
The suction connection and single mounting point to anchor the table in place :
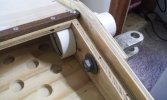
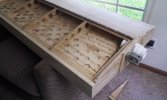
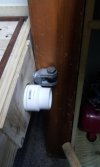
The table can swing and rotate about this single connector . The work top can be level or angled .
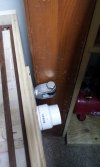
Fitted with standard A/C filters :
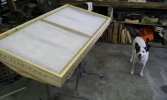
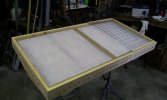
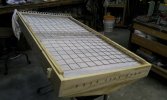
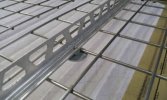
Last edited: