Scratchbuilder
Well-Known Member
- Joined
- Sep 30, 2024
- Messages
- 98
So new forum and to start off my new life here I thought I would start with a Leopard. I could have carried on with some builds I have underway such as the Tiger 1 diorama, but then you would have missed the first half of the builds, and there is nothing more confusing than trying to sort out what was said before and how it was done.
I have the RFM Leopard 2A6M CAN
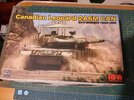
This is to go with the 2A4 CAN version I built some time ago.
Now this like the '4 will have some additions to improve the look of the model, it will have...
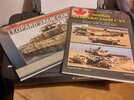
Reference books...
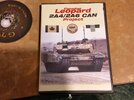
A dvd to pass those hours away while waiting for items to dry...
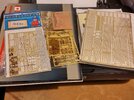
A bit of brass etch to replace a few items and keep the fingers flexible....
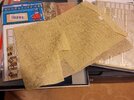
Plus some 'Barracuda' camo netting....
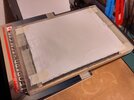
And this - this will be turned into the thermal blanket that goes under the 'Barracuda'....
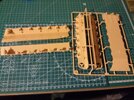
And so the work begins, a bit blurred, but the night is getting on and I need my beauty sleep...
More tomorrow
Cheers
Mike
I have the RFM Leopard 2A6M CAN
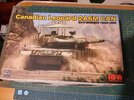
This is to go with the 2A4 CAN version I built some time ago.
Now this like the '4 will have some additions to improve the look of the model, it will have...
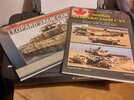
Reference books...
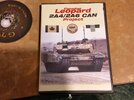
A dvd to pass those hours away while waiting for items to dry...
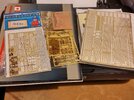
A bit of brass etch to replace a few items and keep the fingers flexible....
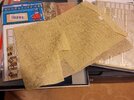
Plus some 'Barracuda' camo netting....
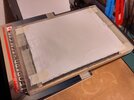
And this - this will be turned into the thermal blanket that goes under the 'Barracuda'....
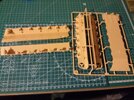
And so the work begins, a bit blurred, but the night is getting on and I need my beauty sleep...
More tomorrow
Cheers
Mike